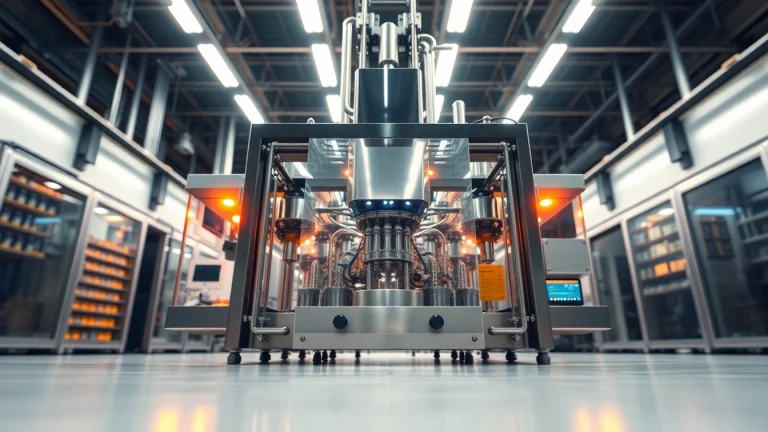
Leading Liquid Packaging Machine Supplier for Optimal Efficiency and Quality
Understanding Liquid Packaging Machines
In the dynamic world of manufacturing and production, liquid packaging machines play an indispensable role in ensuring safe and efficient containment of various liquids and pastes. These machines are designed to automate the filling, sealing, and packaging process, significantly enhancing productivity and minimizing human error in production lines. The adoption of advanced machines has revolutionized industries such as food and beverage, pharmaceuticals, and chemicals. Liquid Packaging Machine Supplier services can facilitate this transition with tailored solutions to meet specific operational needs.
What Are Liquid Packaging Machines?
Liquid packaging machines are specialized equipment designed for the containment, sealing, and labeling of liquid products. These machines can handle a variety of liquids, from thin, free-flowing substances like water and juices to thicker pastes, creams, and gels. The main functions of liquid packaging machines include:
- Filling: Automated or semi-automated processes fill containers with precise measurements of the liquid.
- Sealing: After filling, the containers are sealed securely to ensure product integrity and prevent leakage.
- Labeling: Many machines include labeling systems that apply necessary product information accurately on the packaging.
- Cartoning and Palletizing: Some systems are integrated to package several units in a carton or onto a pallet for transportation.
Types of Liquid Packaging Machines Available
There are several types of liquid packaging machines designed to cater to various operational requirements. Here are the most prominent types:
- Inline Filling Machines: These machines are typically used for high-speed filling in assembly line setups and are ideal for packaging a wide range of products across different industries.
- Piston Filling Machines: These are suitable for viscous products and operate by drawing liquid into a cylinder and dispelling it into containers with precise measurements.
- Aseptic Filling Machines: Designed for products requiring sterile conditions—often used in the food and beverage industry to extend shelf life without preservatives.
- Vacuum Filling Machines: These systems remove air from the packaging before sealing, a critical process to prevent oxidation and spoilage for sensitive liquids.
- Pre-made Pouch Filling Machines: Ideal for products that need a flexible packaging style. These machines fill pouches that have been manufactured before the filling process.
Key Features to Look for in a Supplier
Choosing the right liquid packaging machine supplier is crucial for ensuring quality, reliability, and efficiency in production. Here are some essential features to consider:
- Experience and Expertise: A supplier with a proven track record in the industry can offer invaluable insights and support tailored to your specific needs.
- Quality Assurance: Look for suppliers who adhere to international quality standards, ensuring their machines are built to last and perform consistently.
- Customization Options: Every business has unique requirements; a good supplier should offer customization capabilities to align the machinery with your production goals.
- Technical Support: Ongoing support and maintenance features are crucial for minimizing downtime and optimizing performance.
- Reviews and References: Checking the supplier’s reputation through customer testimonials and case studies can provide insight into their reliability and service.
Benefits of Choosing a Reliable Supplier
Selecting a trustworthy liquid packaging machine supplier not only ensures high-quality equipment but also brings a multitude of long-term advantages. Here are some benefits of working with a reliable supplier:
Quality Assurance and Standards Compliance
Reliable suppliers adhere to stringent quality control measures and compliance with relevant industry regulations. This means machines are less likely to malfunction, resulting in reduced production interruptions and safety risks. Furthermore, equipment meeting high standards is essential for maintaining product quality, crucial in sectors such as food and pharmaceuticals.
Cost-Effectiveness and Long-Term Savings
Investing in high-quality packaging machinery may involve higher upfront costs but leads to substantial long-term savings. Well-built machines typically experience lower maintenance costs, have fewer breakdowns, and can improve operational efficiency, ultimately translating to a more profitable production process. In contrast, cheaper machines may incur hidden costs due to frequent repairs and inefficiency.
Technical Support and Maintenance Services
Working with a reliable supplier often means receiving comprehensive technical support, which is vital for troubleshooting and repairs. Efficient maintenance services minimize downtime, ensuring that production can continue with minimal interruptions. A good supplier provides training for staff so they can handle equipment confidently and competently.
How to Select the Right Liquid Packaging Machine
Choosing the correct liquid packaging machine involves a thorough evaluation of your specific packaging needs, potential equipment performance, and the supplier’s reliability. Here are key points to consider in the selection process:
Assessing Your Packaging Needs
First and foremost, you must understand your specific packaging needs. Consider the following factors:
- Type of Product: Is your liquid thin or thick? Does it contain particulates? The product type influences which machine suits your operations best.
- Production Volume: Assess the desired output volume to ensure the machinery can handle peak production times.
- Container Type: The packaging format can determine which machine is most suitable—whether bottles, pouches, or other formats.
- Regulatory Compliance: Certain products, especially in food and pharmaceuticals, may require compliance with specific regulatory standards, impacting your machine choice.
Evaluating Machine Performance and Specifications
Review the performance metrics and specifications of potential machines thoroughly. Key metrics include:
- Filling Speed: The machine’s speed must align with your production target.
- Accuracy and Precision: For minimizing product waste, machines should offer precise filling capabilities.
- Flexibility: If your production line will change frequently, machines offering changeover flexibility for various products and containers may be necessary.
- Durability: Machines made of high-quality materials spare you from future replacements and frequent repairs.
Supplier Reputation and Customer Reviews
Before finalizing a supplier, investigating their reputation is essential. Customer reviews and case studies can shed light on the supplier’s service reliability and the performance of their machines in real-world scenarios. Industry forums, social media platforms, or personal references can provide further insights into supplier trustworthiness.
Innovations in Liquid Packaging Technology
The liquid packaging industry has seen significant advancements, driven by technology and evolving consumer preferences. These technological innovations not only enhance efficiency but also respond to sustainability concerns and changing market demands.
Trends Shaping the Future of Liquid Packaging
The packaging machinery of the future will increasingly leverage technology and consumer behavior analytics. Notable trends currently shaping the industry include:
- Smart Machines: Incorporating IoT (Internet of Things) technology, modern machines can monitor performance in real time, optimizing production processes and predictive maintenance schedules.
- Customizable Solutions: More packages are made to order, requiring suppliers to adopt scalable machines accommodating various shapes, sizes, and output rates.
- Automation: Fully automated packing lines are becoming the standard, improving efficiency and executing high-volume packing with minimal manual labor.
Impact of Automation on Packaging Efficiency
The automation of liquid packaging processes delivers significant benefits, including increased line speeds, reduced labor costs, and improved consistency in packaging quality. Automated systems reduce the potential for human error, streamline operations, and allow for better tracking and reporting of production data, leading to more informed decision-making regarding process improvements.
Sustainability Practices in Packaging Solutions
Sustainability is increasingly central to the packaging industry, driven by consumer demand for eco-friendly practices. Innovations include the use of biodegradable materials, energy-efficient manufacturing processes, and machinery that supports recyclable packaging formats. Many suppliers are striving to provide solutions that align with global sustainability goals while meeting business needs.
Frequently Asked Questions about Liquid Packaging Machines
How do I choose the right machine for my product?
Choosing the right machine involves understanding your specific product characteristics, the required filling volume, and selecting a machine suited to your packaging format and compliance needs. Consulting with a reliable supplier who understands your industry can greatly enhance the selection process.
What should I expect during installation?
Installation processes typically involve site evaluations, equipment setup, calibration for optimal operational efficiency, and training for your operational team. A qualified supplier will provide detailed guidance and support during this phase of deployment to ensure a smooth transition.
How can I ensure ongoing machine efficiency?
To maintain optimal performance, adhere to routine maintenance schedules recommended by your machine supplier. This includes regular inspections, timely parts replacements, and using recommended maintenance protocols. Training staff appropriately on best practices and operating procedures also ensures that equipment runs efficiently at all times.