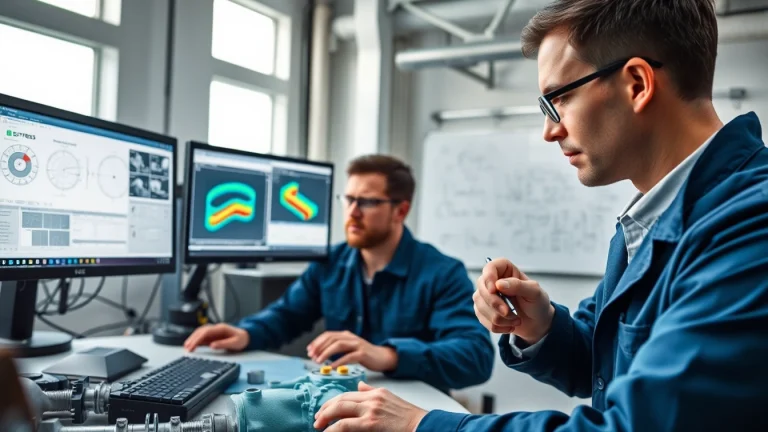
Elevating Precision: Your Guide to Choosing the Right Pipe Stress Analysis Company
Understanding Pipe Stress Analysis
What is Pipe Stress Analysis?
Pipe stress analysis is a crucial engineering process used to evaluate the behavior of piping systems subjected to various forces and moments during operation. This analysis plays a significant role in ensuring the structural integrity of pipelines within industrial settings by predicting how materials respond to thermal expansions, vibrations, and other load factors. By using sophisticated software and techniques, engineers can simulate the simulated impacts on pipes in real-world conditions to avoid failures that can be costly and hazardous.
Importance of Accurate Stress Analysis
Accurate stress analysis is vital both for safety and efficiency within industries relying on extensive piping systems. Any failure in these systems can lead to pipeline ruptures, leaks, and potential environmental disasters. Furthermore, conducting thorough analyses helps in complying with safety regulations and industry standards. The implications of neglecting pipe stress analysis can lead to catastrophic failures, loss of productivity, and substantial financial losses. In light of these risks, selecting a competent pipe stress analysis company becomes crucial for effective project management and resource optimization.
Common Applications in Various Industries
Pipe stress analysis is applicable in various sectors, including:
- Oil and Gas: Assessing the impact of thermal expansion and cycle loading on pipelines.
- Chemical Manufacturing: Ensuring piping systems can withstand corrosive materials without compromising safety.
- Power Generation: Validating the integrity of steam and water systems under high pressure.
- Pharmaceuticals: Maintaining cleanliness and integrity while adhering to stringent regulations.
- Water Systems: Ensuring the stability and sustainability of water distribution networks.
Evaluating Pipe Stress Analysis Companies
Key Factors to Consider When Choosing
When evaluating a pipe stress analysis company, it’s essential to consider several factors that contribute to their efficacy:
- Experience: Years in operation and expertise in specific industry sectors.
- Technology Use: Proficiency in advanced software tools essential for accurate modeling.
- Compliance Knowledge: Understanding of local and international codes and standards.
- Customization: Ability to tailor services to meet specific project requirements.
Industry Reputation and Client Feedback
Assessing a company’s reputation and client feedback can provide invaluable insights into their reliability. Checking for online testimonials, case studies, and references can unveil how other clients have benefited from their services. Industry awards and recognitions can also serve as indicators of excellence and credibility.
Certifications and Qualifications to Look For
Certifications from recognized authorities can often differentiate reputable companies from lesser-known firms. Look for qualifications pertaining to:
- Registered Professional Engineer (PE) status
- Certification in piping design and analysis (e.g., ASME, API)
- Quality management system certifications (e.g., ISO 9001)
Best Practices in Pipe Stress Analysis
Methodologies Employed by Leading Companies
Leading pipe stress analysis companies typically employ various methodologies to ensure precision and accuracy. Common methodologies include:
- Finite Element Analysis (FEA): This method breaks down complex piping systems into smaller, manageable parts to analyze stress and deformation.
- Dynamic Analysis: Evaluating responses under time-dependent loads such as seismic events or transient pressure surges.
- Thermal Expansion Considerations: Addressing changes caused by temperature variations within the installed systems.
Tools and Technologies Used
Successful pipe stress analysis relies greatly on advanced tools and technologies. Some of the most recognized include:
- CAESAR II: A widely used software for piping stress analysis that accommodates complex geometries.
- AutoPIPE: This software aids in modeling various pipe configurations ensuring compliance with global standards.
- ANSYS: Offers robust simulation tools applicable for multi-physics analysis.
Case Studies of Successful Implementations
Examining case studies can reveal best practices and successful implementations of pipe stress analysis. Here, we explore examples from various industries:
- Petrochemical Plant: A case study illustrates how a company employed FEA to optimize pipe routing, reducing material costs while enhancing safety.
- Power Plant: Specific projects utilized dynamic analysis during seismic retrofitting, ensuring compliance with safety standards while maintaining operational efficiency.
Common Challenges in Pipe Stress Analysis
Identifying Potential Risks
Pipe stress analysis is not without its challenges. Recognizing potential risks can facilitate a proactive approach to mitigation:
- Design Misalignment: Incorrect design layouts can lead to stress concentrations.
- Material Misjudgments: Using improper materials can compromise system integrity.
- Insufficient Data: Lack of reliable input data may lead to incorrect analysis outcomes.
Solutions to Overcome Challenges
To address the challenges faced in pipe stress analysis, several solutions can be implemented:
- Integrating thorough data collection methods early in the design phase.
- Regular training for engineers to stay updated with the latest methodologies and tools.
- Collaboration with specialists in material science to ensure the use of appropriate materials.
Staying Compliant with Industry Standards
Maintaining compliance with industry standards is paramount for any project. Companies must stay informed about relevant codes such as ASME B31.3 for process piping and API 570 for piping inspection. Regular audits and updates can ensure continued adherence to evolving safety regulations.
Measuring Success with Pipe Stress Analysis
Key Performance Indicators to Monitor
Monitoring key performance indicators (KPIs) can quantify the effectiveness of pipe stress analysis:
- System Reliability: Measurement of incidents over a defined period.
- Cost Savings: Evaluating reductions in maintenance and repair expenses due to preemptive analyses.
- Regulatory Compliance: The number of compliance violations noted after inspections.
Integrating Analysis Results into Operations
Effective integration of analysis results into operational processes is crucial for maximizing benefits. Implementation may include:
- Developing action plans based on findings to adjust designs or operational practices.
- Training staff in the implications of stress analysis findings to ensure appropriate responses.
- Establishing regular review processes for incorporating analysis into ongoing operational strategies.
Continuous Improvement Strategies
Adopting a culture of continuous improvement can significantly amplify the benefits of pipe stress analysis. Strategies may involve:
- Periodic reviews of performance data to identify improvement areas.
- Encouraging feedback from employees involved in day-to-day operations regarding the effectiveness of implemented strategies.
- Investing in new technologies and methodologies to enhance analysis precision and reliability.