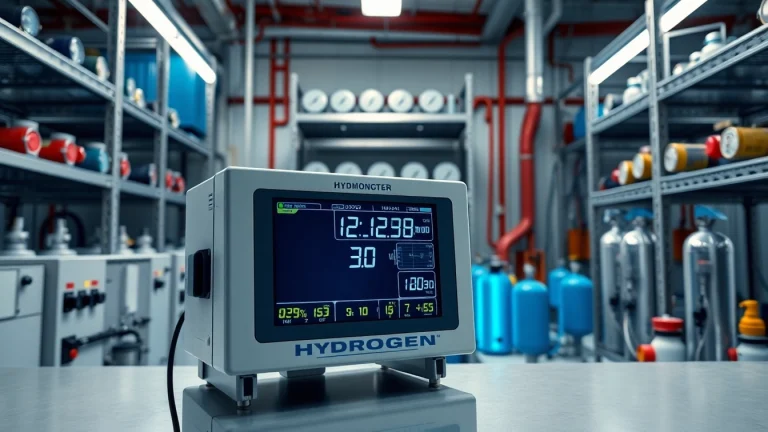
Essential Insights on Hydrogen Monitors: Enhancing Safety and Efficiency
Understanding Hydrogen Monitors
What is a Hydrogen Monitor?
A hydrogen monitor is a specialized device designed to detect and measure the concentration of hydrogen gas in the atmosphere. These instruments are critical in various industries, particularly those involving processes where hydrogen is produced, stored, or utilized, such as in petrochemicals, refining, and metal production. The monitoring of hydrogen is vital due to its flammability, potential for explosion in certain concentrations, and its importance in maintaining safety and efficiency in industrial operations. An effective hydrogen monitor provides real-time data and alerts to operators, enabling swift responses to hazardous situations.
How Hydrogen Monitors Work
Hydrogen monitors operate based on several detection technologies that allow them to sense hydrogen concentrations in the air. Common methods include:
- Electrochemical Detection: This method involves a chemical reaction that produces an electrical current proportional to the hydrogen concentration. It is favored for its sensitivity and accuracy.
- Metal-Oxide Sensors: These sensors use a semiconductor material that changes resistance when exposed to hydrogen, allowing for the detection of its presence.
- Infrared Spectroscopy: This technique measures the absorption of infrared light by gas molecules, which can be calibrated to detect specific gases, including hydrogen.
Regardless of the technology used, hydrogen monitors are calibrated to provide real-time readings, and many include data logging capabilities for further analysis.
Types of Hydrogen Monitors Available
Hydrogen monitors can be categorized based on their specific use cases and features. Here are the primary types:
- Portable Hydrogen Monitors: These are handheld devices designed for personal safety or fieldwork. They often feature alarms to alert users to hazardous hydrogen levels.
- Fixed Hydrogen Monitors: Installed at specific locations, these devices continuously monitor hydrogen levels in a designated area and provide data to a central control system.
- Wireless and Networked Monitors: These advanced devices can communicate with other security systems and provide remote monitoring capabilities.
Selecting the appropriate type of hydrogen monitor depends on the specific application, workplace environment, and safety requirements.
Importance of Hydrogen Monitoring
Safety Regulations and Compliance
In many industries, safety regulations mandate the monitoring of hydrogen levels to prevent accidents. Regulatory bodies such as OSHA (Occupational Safety and Health Administration) and NFPA (National Fire Protection Association) have established guidelines to protect workers from the risks associated with hydrogen exposure. Compliance with these regulations not only ensures a safe working environment but also helps to avoid costly fines and legal repercussions.
Impact on Industrial Processes
Effective hydrogen monitoring directly influences operational efficiency. Hydrogen is essential in various industrial applications, including hydrogenation in the food industry, hydrotreating and hydrocracking in refineries, and as a feedstock in chemical manufacturing. Monitoring systems help maintain the right hydrogen levels, enhancing product quality, minimizing downtime, and supporting efficient chemical reactions. Moreover, proactive monitoring enables early detection of leaks, reducing waste and promoting sustainability.
Environmental Considerations
Monitoring hydrogen levels also has significant environmental implications. Hydrogen, while a clean fuel, can contribute to greenhouse gas emissions through incomplete combustion. By maintaining optimal hydrogen levels and ensuring complete combustion in processes, industries can minimize their environmental footprint. Additionally, effective hydrogen monitoring plays a role in transitioning to green hydrogen production, reducing reliance on fossil fuels, thus fostering a more sustainable future.
Selecting the Right Hydrogen Monitor
Key Features to Look For
When choosing a hydrogen monitor, consider the following key features:
- Sensitivity and Range: The sensitivity level and detection range of the monitor are crucial. Different applications may require varying sensitivity levels based on the potential hydrogen concentration.
- Response Time: A quick response time ensures that any increases in hydrogen levels are detected and addressed promptly.
- Alarm Systems: Integrated alarm systems, with both visual and audible alerts, are essential to notify operators of dangerous conditions.
- Data Logging and Connectivity: Many modern monitors provide data logging capabilities and connectivity options for integration into larger safety systems.
- Durability and Environmental Rating: Ensure the monitor is suitable for the environment it will operate in. Industrial settings may require more robust and rugged devices.
Costs and Budgeting
The cost of hydrogen monitors can vary widely based on technology, features, and manufacturer reputation. Basic portable units may be available for a few hundred dollars, while advanced fixed systems can range into the thousands. When budgeting for hydrogen monitoring solutions, consider the long-term benefits of safety, compliance, and efficiency improvements against the initial investment. It is also wise to account for maintenance costs to ensure long-term reliability.
Trusted Brands and Models
Several brands are recognized in the hydrogen monitoring market for their reliability and innovation. Brands such as Dräger, RKI Instruments, and Honeywell offer a range of models tailored to diverse industrial needs. When selecting a model, research product reviews, specifications, and user feedback to ensure it meets your facility’s specific requirements.
Implementing Hydrogen Monitoring Solutions
Installation Guidelines
Proper installation of hydrogen monitors is essential for their optimal function. Key guidelines include:
- Location: Install monitors at potential leak points and in areas where hydrogen is used, produced, or stored.
- Height: Placement height is important; position monitors according to the physical behavior of hydrogen (it is lighter than air).
- Calibration: Regular calibration is necessary for maintaining accuracy; follow the manufacturer’s recommendations.
Maintenance Practices
Routine maintenance is vital for reliable operation of hydrogen monitors. Maintenance practices should include:
- Regular Testing: Conduct regular tests to ensure the monitor is functioning correctly and providing accurate readings.
- Battery Replacement: If applicable, replace or recharge batteries as per guidelines to ensure continuous operation.
- Sensor Replacement: Follow manufacturer’s guidelines for sensor lifespan and replacement to avoid performance degradation.
Training for Effective Use
Training staff on using hydrogen monitoring equipment can significantly enhance safety and efficiency. Training should cover:
- Operational Training: Ensure staff understands how to operate the monitor, interpret readings, and respond to alarms.
- Emergency Protocols: Employees should be trained on emergency procedures in case of hydrogen exposure or leaks.
- Maintenance Training: Key personnel should receive training on the upkeep and calibration procedures for hydrogen monitors.
Future Trends in Hydrogen Monitoring Technology
Innovations in Sensor Technology
Recent advancements in sensor technology are paving the way for more accurate, sensitive, and durable hydrogen monitors. The emergence of nanomaterials and innovative sensor designs may improve detection capabilities while lowering production costs. Future sensors may offer enhanced selectivity, reducing false alarms and increasing reliability in complex industrial environments.
Integration with Smart Systems
The Internet of Things (IoT) is revolutionizing monitoring systems, including hydrogen detection. Smart hydrogen monitors can now connect to central control systems, allowing for real-time data visualization and analysis. Integration with smart buildings and industrial automation systems can enhance safety protocols, streamline operations, and facilitate predictive maintenance.
Predictive Analytics and Data Management
With the rise of big data analytics, hydrogen monitors can contribute to predictive maintenance strategies. Advanced data analysis techniques can provide insights into usage patterns, performance metrics, and potential failure points. This data-driven approach enables organizations to anticipate maintenance needs proactively and improve overall safety and efficacy in hydrogen handling operations.