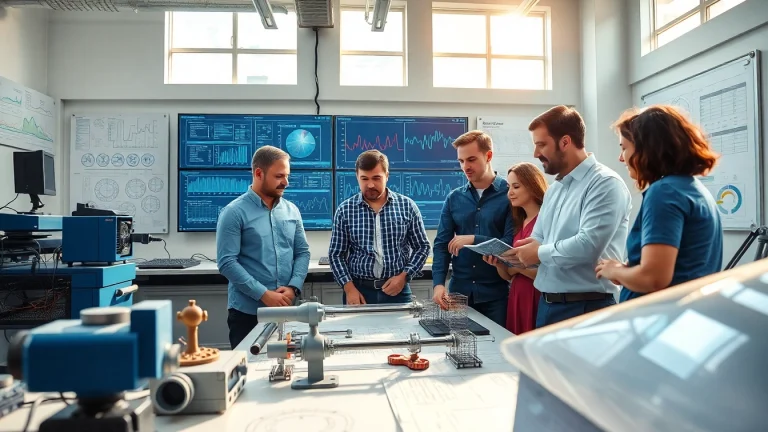
Optimizing Pipe Stress Analysis for Your Company: Best Practices and Strategies
Understanding Pipe Stress: What is it and Why it Matters
Defining Pipe Stress
Pipe stress refers to the internal and external forces acting on pipes in various systems, particularly in industries like oil and gas, chemical processing, and power generation. These stresses can arise from changes in temperature, pressure, and even operational conditions such as vibrations. Proper management of pipe stress is crucial, as it ensures the integrity and longevity of the piping systems. Failure to address pipe stress can lead to system malfunctions, leaks, or catastrophic failures, underscoring the importance of having a reliable pipe stress Company, in place.
Impacts on System Integrity
Pipe stress can contribute to several critical issues affecting overall system integrity. These issues include:
- Material Fatigue: Repeated exposure to stress can weaken pipe material, leading to cracks or eventual rupture.
- Decreased Service Life: Excessive stress can significantly reduce the operational lifespan of a piping system.
- Compromised Safety: Stress-related failures can pose serious safety risks for personnel and nearby facilities, making stress analysis essential.
- Increased Maintenance Costs: Regular inspections and repairs driven by stress-induced failures can inflate operational costs.
Common Industry Standards
Various standards and codes govern the engineering and analysis of pipe stress to ensure consistency and safety. Some of the most widely recognized standards include:
- ASME B31.1: This code provides guidelines for power piping, focusing on the safe construction and operation of piping systems.
- ASME B31.3: This standard pertains to process piping in chemical facilities, detailing stress analysis criteria relevant to the industry.
- API 570: The American Petroleum Institute’s code targets inspection, repair, and alteration of piping systems in the petrochemical industries.
Understanding these standards ensures that your pipe stress analysis aligns with industry requirements, facilitating improved safety and compliance.
Factors Affecting Pipe Stress in Engineering
Temperature Fluctuations
Temperature changes can significantly affect pipe stress, as they directly influence material properties and the physical behavior of piping systems. When temperatures rise, pipes expand; conversely, they contract when temperatures drop. The variation in these thermal expansions must be carefully managed to prevent stresses that exceed material strength limits.
In industries like oil and gas, where operating temperatures can fluctuate drastically, effective thermal management strategies, such as the implementation of expansion loops and supports, can alleviate excessive stresses.
Pressure Variations
Pressure changes are another critical factor that impacts pipe stress. Increased pressure within a pipe can lead to additional tensile stress, which, if not properly accounted for, may result in a failure of the pipe material. The design and analysis of piping systems must include calculations for maximum expected pressures to ensure the appropriate thickness and material selection.
Pressure fluctuations might occur due to varying operational conditions or even external forces, emphasizing the need for regular monitoring and adjustments.
Material Selection
The choice of materials used in pipe construction plays a vital role in stress management. Different materials exhibit varying levels of strength, ductility, and resistance to corrosion and fatigue.
For example, popular materials such as carbon steel, stainless steel, and plastic have distinct properties that make them suitable for specific applications. Engineers must consider the environmental conditions and stressors the material will face in operation to optimize performance and durability.
Tools and Software for Pipe Stress Analysis
Leading Industry Applications
The complexity of pipe stress analysis requires the use of specialized software tools that are designed to simulate conditions, analyze stress, and predict potential failures. Some of the most widely adopted applications in the industry include:
- CAESAR II: A leading software tool for pipe stress analysis, which provides extensive modeling capabilities and powerful output visualization, making it easy for engineers to interpret the results.
- AutoPIPE: This software allows for innovative modeling features and stress analysis of piping systems, optimized for both thermal and pressure assessments.
- ANSYS: While widely recognized for its general simulation capabilities, ANSYS also supports advanced modeling of piping systems for detailed structural analysis and assessments.
Integrating Software into Workflow
Integrating stress analysis software into the project workflow is crucial for maximizing efficiency. It involves coordinating between design teams, construction crews, and plant operations to ensure continuous feedback and improvement. Training personnel to effectively use these applications helps streamline the analysis process, reduces errors, and speeds up project timelines.
Additionally, a collaborative environment allows for real-time data sharing, which is crucial for identifying stressful conditions and implementing required adjustments without significant delays.
Best Tools for Accuracy
Accuracy in pipe stress analysis relies heavily on the tools utilized. Best tools are characterized by:
- User-Friendly Interfaces: Tools should have intuitive designs that facilitate easy navigation and functionality.
- Comprehensive Data Libraries: Access to extensive material databases allows engineers to select appropriate materials effortlessly.
- Extensive Documentation: Reliable documentation and support play a vital role in ensuring engineers can make informed decisions based on software capabilities.
Choosing the right tools can significantly mitigate risks associated with inaccurate stress predictions and improve overall project outcomes.
Case Studies: Successful Pipe Stress Management
Real-World Applications
Practical applications of pipe stress analysis illustrate the critical role it plays in various industries. One notable case included a major oil refinery, which invested in a comprehensive pipe stress analysis as part of its expansion project. By utilizing advanced software and undergoing thorough evaluations, the facility successfully mitigated potential failures and optimized operations.
Another example can be drawn from a chemical processing plant, where thermal expansions posed risks to the integrity of the piping system. By implementing effective expansion loops and enhanced supports based on detailed stress analysis, the facility saw a reduction in maintenance costs and an increase in efficiency.
Lessons Learned from Failures
While successful case studies provide insights into effective management, failures also offer valuable lessons. One infamous incident was the rupture of a high-pressure gas pipeline due to undetected stress concentrations. An inadequate stress analysis and material selection resulted in catastrophic failure, highlighting the importance of investing in rigorous stress testing and compliance with industry standards.
Through such unfortunate events, the industry has learned the significance of thorough pre-emptive measures to address stress before systems become operational.
Best Practices for Implementation
Implementing pipe stress management requires adherence to best practices, which include:
- Conduct Regular Inspections: Ongoing assessments help detect potential stress issues before they escalate.
- Use Advanced Software: Leverage reliable analysis software to ensure precise calculations and modeling.
- Enhance Collaboration: Foster teamwork between engineering, construction, and operation teams to enable proactive communication and resolve potential stress issues efficiently.
By incorporating these practices, companies can reduce the likelihood of stress-related failures and ensure a more reliable piping system.
Future Trends in Pipe Stress Analysis
Advancements in Technology
The future of pipe stress analysis is being shaped by rapid advancements in technology. Innovations such as Artificial Intelligence (AI) and Machine Learning (ML) are beginning to influence the efficiency and accuracy of stress analyses. By utilizing predictive analytics, engineers can forecast stress conditions and manage risks proactively.
Additionally, the integration of the Internet of Things (IoT) allows real-time monitoring of piping systems, providing immediate data on stress parameters. This capability equips companies to make data-driven decisions rapidly, improving response times and operational efficiency.
Regulatory Changes and Compliance
The continuous evolution of industry standards also impacts pipe stress analysis. As regulatory bodies impose stricter guidelines to enhance safety and reliability, companies must stay abreast of these changes to remain compliant. Adapting to evolving regulations requires constant updates to internal protocols and procedures, reinforcing the necessity for an agile and informed approach to stress analysis.
Preparing for Industry Shifts
As industries evolve, engineers and stakeholders must prepare for significant shifts in technology, regulations, and operational paradigms. The increasing emphasis on sustainability and environmental impact is likely to influence material selection and design considerations. Companies that effectively anticipate these shifts will enhance their competitive edge and ensure long-term viability in an ever-changing landscape.